The Power of Materialise in Revolutionising 3D Printing for Modern Businesses
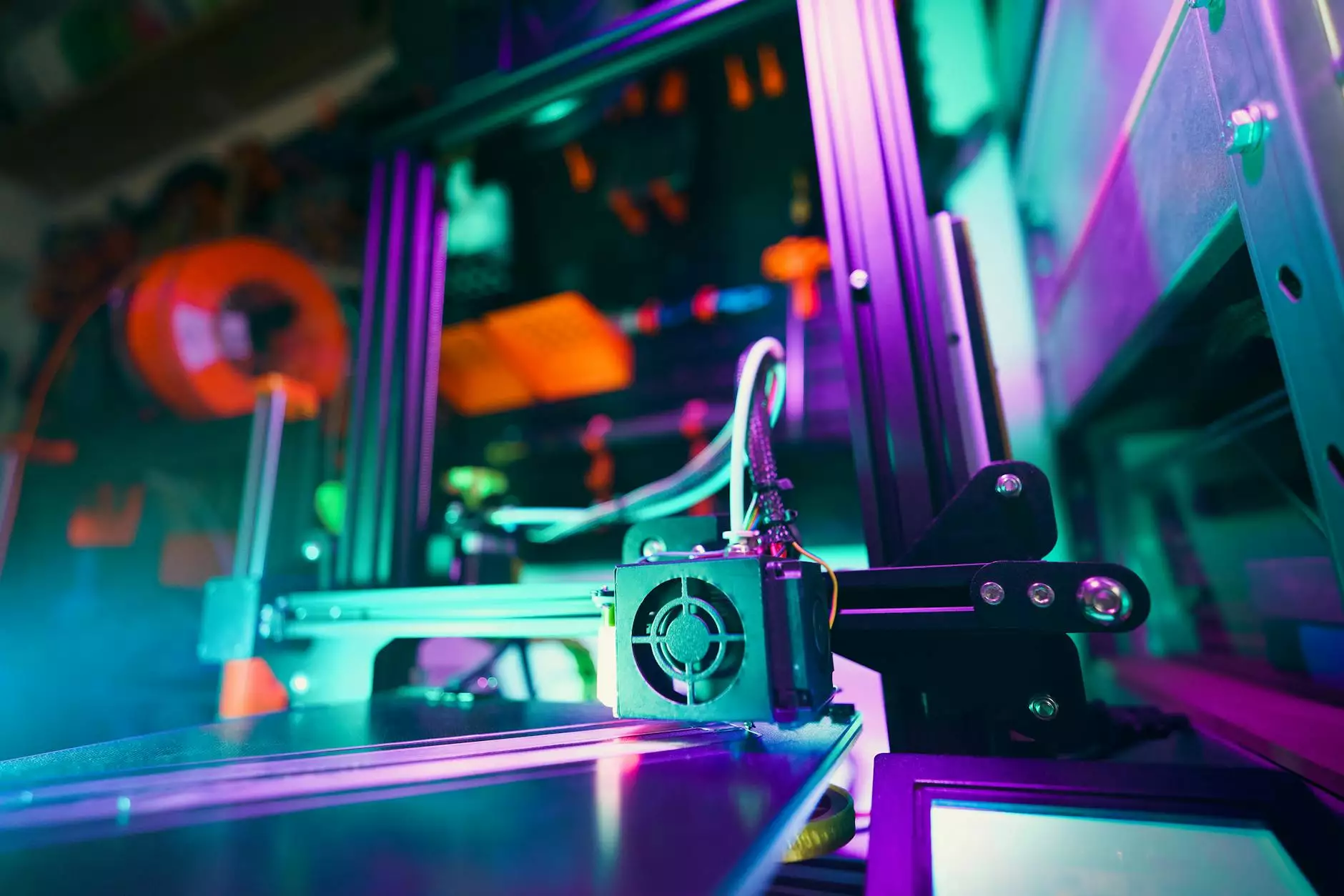
In an era where innovation drives competitive advantage, the application of materialise technology in 3D printing has emerged as a game-changer for countless industries. From manufacturing and healthcare to automotive and aerospace, businesses are harnessing the transformative potential of materialise to create intricate designs, accelerate prototypes, and produce custom components with unparalleled efficiency and precision. This comprehensive guide explores the significance of materialise within the realm of 3D printing, detailing how it fosters sustainable growth, enhances product development, and propels industries into the future of manufacturing excellence.
Understanding Materialise: The Backbone of Advanced 3D Printing Solutions
At its core, materialise refers to the process of transforming digital models into tangible physical objects through additive manufacturing technologies. The term is synonymous with innovation, precision, and adaptability—characteristics that define the modern capabilities of 3D printing. When integrated into business operations, materialise enables companies to turn concepts into reality faster than traditional manufacturing methods, reducing time-to-market and fostering agility in design iterations.
The Role of Materialise in Enhancing Product Development Cycles
Accelerating Prototyping and Iterative Design
One of the most profound impacts of materialise in 3D printing is its ability to radically shorten product development cycles. Companies no longer need to wait weeks or months for tooling and manufacturing but can instead produce functional prototypes within days. This rapid prototyping not only enhances innovative capacity but also facilitates multiple design iterations, enabling teams to refine aesthetics, functionality, and user experience with remarkable speed.
Cost Effectiveness and Resource Optimisation
Traditional manufacturing often involves significant material waste and high costs associated with tooling and setup. However, materialise allows businesses to optimise material usage, reduce waste, and lower production costs. The additive nature of 3D printing means components are built layer by layer, using only the necessary material, which aligns perfectly with sustainable manufacturing objectives.
Key Industries Benefiting from Materialise and 3D Printing
Healthcare and Medical Devices: Precision Meets Customisation
In healthcare, materialise has unlocked new possibilities for personalised medicine, custom implants, and prosthetics. 3D printed medical models allow surgeons to plan complex surgeries with greater accuracy, leading to better patient outcomes. Moreover, materialise processes enable the production of patient-specific implants that perfectly match individual anatomical structures, reducing surgery times and improving overall effectiveness.
Automotive and Aerospace: Lightweight and Complex Components
The automotive and aerospace sectors benefit immensely from materialise by producing lightweight components that do not compromise strength or durability. Complex geometries that are impossible to achieve with traditional manufacturing are now feasible, enabling advanced aerodynamic designs and fuel-efficient solutions. The rapid production of prototypes and small batch runs also accelerates innovation cycles in these high-tech industries.
Manufacturing and Industrial Applications: Enhancing Precision and Flexibility
Manufacturers leverage materialise to streamline production processes, create tools and jigs, and develop customised parts quickly. The flexibility of 3D printing affords direct manufacturing on demand, reducing inventory costs and enabling just-in-time production models. Companies can respond swiftly to market demands and customise products at individual or batch levels without costly retooling.
The Unique Advantages of Incorporating Materialise Solutions
- Unmatched Design Freedom: Create complex geometries and intricate details that are otherwise impossible with traditional manufacturing techniques.
- Reduced Lead Times: Transition from digital design to physical prototype or final component swiftly, speeding up project timelines.
- Lower Production Costs: Save on tooling, labour, and material wastage, leading to increased profitability.
- Customisation and Personalisation: Deliver tailored products or components to meet specific customer needs or specialised applications.
- Sustainability: Less waste and energy consumption boost the ecological footprint of manufacturing processes.
- Remote Production Capabilities: Use digital files to produce parts anywhere with access to 3D printers, expanding geographical reach.
Implementing Materialise in Your Business Strategy
Choosing the Right 3D Printing Technologies
Different applications necessitate specific 3D printing methods, such as Stereolithography (SLA), Selective Laser Sintering (SLS), Fused Deposition Modelling (FDM), or Electron Beam Melting (EBM). Determining the optimal technology depends on factors like material requirements, precision, surface finish, and production volume. Materialise specialises in integrating these advanced techniques seamlessly into business workflows to maximise ROI.
Selecting Appropriate Materials for Your Needs
Materialise offers a vast array of materials tailored for diverse applications, including plastics, metals, composites, and bio-materials. The choice of material impacts the durability, flexibility, heat resistance, and biocompatibility of produced parts. By carefully selecting the right material, companies can ensure the end product meets both technical and regulatory standards.
Design for Additive Manufacturing (DfAM)
A crucial aspect of leveraging materialise is designing components specifically for 3D printing. DfAM practices optimise geometry for manufacturability, reduce assembly complexity, and take advantage of complex structures such as lattice frameworks and internal channels. Investing in skilled design teams or consulting with materialise experts maximises the benefits of additive manufacturing.
Future Trends and Innovations Powered by Materialise
Integration of Artificial Intelligence and Machine Learning
The future of materialise in 3D printing will see increased utilisation of AI and machine learning to optimise design, predict material performance, and automate workflows. These innovations promise to further reduce production times and improve product quality.
Development of New Materials
Continuous research into novel materials, including bio-compatible, conductive, and self-healing composites, will expand the application scope of materialise. These advanced materials will open avenues for innovations in electronics, medicine, and sustainable manufacturing.
Enhanced Digital Manufacturing Ecosystems
The integration of 3D printing with digital supply chains, IoT, and cloud-based platforms will create interconnected ecosystems where materialise solutions can be monitored, managed, and scaled globally. This connectivity ensures real-time feedback, quality control, and rapid response to market needs.
Why Businesses Should Partner with Experts Like infotron.com.tr for Materialise Solutions
Partnering with a reputable provider such as infotron.com.tr ensures access to cutting-edge materialise technologies, expert guidance, and customised solutions aligned with your industry goals. Such collaborations enable businesses to not only adopt 3D printing effectively but also to innovate continually, maintain a competitive edge, and achieve sustainable growth in today's fast-paced market environment.
Conclusion: Embracing the Power of Materialise for a Future-Ready Business
In conclusion, the incorporation of materialise within your company's strategic framework represents a forward-thinking approach to manufacturing and product development. It offers a multitude of advantages—speed, cost savings, design freedom, and customisation—that are essential for thriving in an increasingly competitive landscape. As 3D printing technologies continue to evolve, those who leverage materialise effectively will be at the forefront of innovation, leading the way into a sustainable and highly efficient future of industry.
Whether you are looking to optimise existing processes, develop new products, or explore emerging applications, partnering with specialists like infotron.com.tr will position your business to unlock the full potential of materialise in 3D printing.