The Advanced Innovations of the Electric Injection Moulding Machine
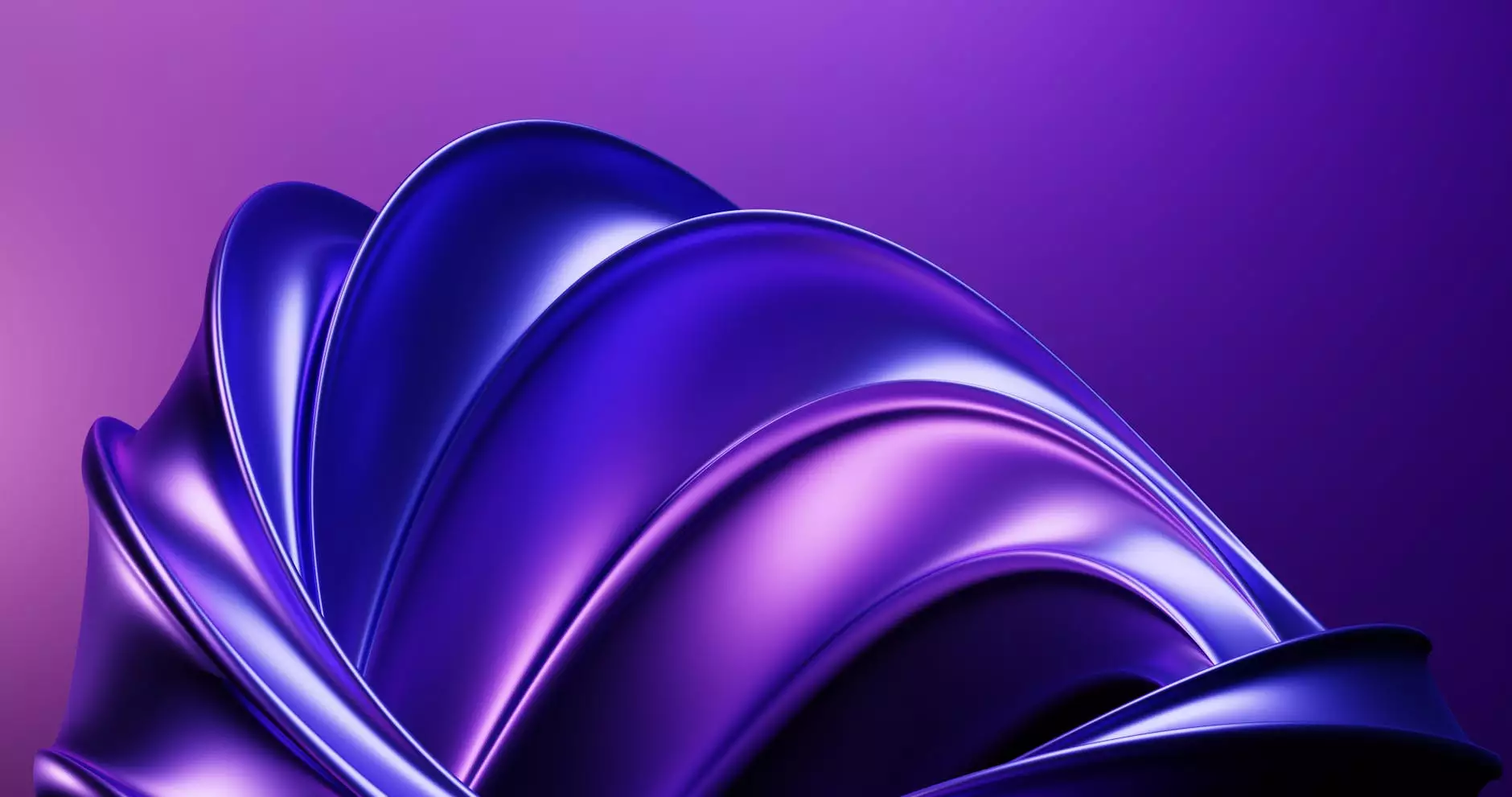
The world of manufacturing is undergoing a significant transformation, driven by technological advancements in machinery and production processes. One of these groundbreaking innovations is the electric injection moulding machine, which has set new benchmarks for efficiency, precision, and sustainability in the metal fabrication industry. This article delves into the myriad benefits, applications, and future potential of electric injection moulding machines, highlighting how they are revolutionizing production processes across various sectors.
Understanding Electric Injection Moulding Machines
To grasp the impact of electric injection moulding machines, it's essential to first understand what they are. These machines utilize electric power to drive all their movements, unlike traditional hydraulic systems that rely on fluids. This transition from hydraulic to electric has ushered in a host of advantages that cater to modern industry demands.
Key Components of Electric Injection Moulding Machines
- Injection Unit: This is responsible for melting and injecting plastic material into the mould. It features precise temperature control to ensure optimal melting.
- Clamping Unit: This component holds the mould in place under pressure, ensuring that the moulded part adheres to specifications.
- Electric Drive System: Utilizing servo motors, this system enables accurate control of speed and position, resulting in enhanced precision.
- Control Panel: Advanced touch-screen panels provide operator guidance and real-time data for monitoring and management.
Benefits of Electric Injection Moulding Machines
The introduction of electric injection moulding machines brings numerous advantages, especially in sectors requiring high precision and low environmental impact. Below are some of the most significant benefits:
1. Enhanced Energy Efficiency
Electric machines consume less energy compared to their hydraulic counterparts. With energy efficiency being a growing concern for industries, the electric injection moulding machine sets a new standard. The servo motors only draw power when needed, reducing overall operational costs.
2. Superior Precision and Repeatability
With advanced motion control and the absence of hydraulic fluctuations, these machines deliver exceptional precision. Each cycle can achieve the same result with high repeatability, which is crucial in industries where slight deviations can lead to significant losses.
3. Environmentally Friendly
Electric injection moulding machines produce minimal waste and utilize less cooling water, resulting in a lower carbon footprint. They also eliminate the use of hydraulic oil, which can be harmful to the environment.
4. Quieter Operation
Unlike hydraulic machines that produce considerable noise during operation, electric moulding machines operate quietly. This is particularly advantageous in environments where noise levels must be controlled.
5. Lower Maintenance Requirements
Electric injection moulding machines require less maintenance due to the absence of hydraulic fluid and the complexity associated with it. This can result in reduced downtime and increased productivity over the machine's lifespan.
Applications of Electric Injection Moulding Machines
Electric injection moulding machines have found applications in a variety of sectors, demonstrating their versatility and effectiveness:
1. Automotive Industry
From dashboards to components inside engines, precision is key in the automotive sector. Electric injection moulding machines provide the accuracy needed for high-quality production.
2. Consumer Electronics
Within the consumer electronics field, the demand for intricate parts with precise tolerances can be met effectively with electric injection moulding, ensuring aesthetic appeal and functional reliability.
3. Medical Devices
The production of medical devices often requires compliance with stringent regulations. Electric injection moulding machines can ensure consistent quality while streamlining the manufacturing process.
4. Packaging Solutions
In packaging, the need for rapid production alongside quality control is paramount. Electric machines can meet these demands effectively, offering customization and shorter lead times.
Choosing the Right Electric Injection Moulding Machine
With various electric injection moulding machines on the market, selecting the right one for your needs can be challenging. Here are some factors to consider:
1. Production Volume
Consider the volume of products you intend to manufacture. Machines come in different sizes, and your choice should align with your production targets.
2. Product Specifications
Evaluate the specific requirements of your product design. Features such as clamping force and injection capacity are crucial metrics in ensuring optimal results.
3. Supplier Reputation
Investigate the reputation of the machine manufacturer. A supplier with extensive experience in the market and strong customer support can make a significant difference in your operational efficiency.
4. Technological Features
Look for machines equipped with advanced technology such as real-time monitoring and automation options. These can enhance productivity and reduce human error.
The Future of Electric Injection Moulding Machines
The trajectory of electric injection moulding machines points towards even more innovation. As technology continues to advance, the integration of artificial intelligence and machine learning can lead to smarter machines that autonomously optimize manufacturing processes.
Moreover, as industries strive for sustainability, electric injection moulding technologies will likely play a central role in reducing environmental impact through improved energy efficiency and reduced emissions.
Conclusion: Embracing the Evolution of Manufacturing with Electric Injection Moulding Machines
The transition to electric injection moulding machines is not just a trend; it represents a fundamental shift towards greater efficiency, precision, and sustainability in manufacturing. As industries evolve and consumer demands shift, investing in electric technology is essential for staying competitive.
Deepmould.net stands at the forefront of these innovations, offering solutions that not only enhance productivity but also align with modern sustainability goals. By embracing electric injection moulding machines, manufacturers can ensure they are equipped to meet the challenges of tomorrow's market.