The Advantages of Accurate Molded Plastics in Modern Manufacturing
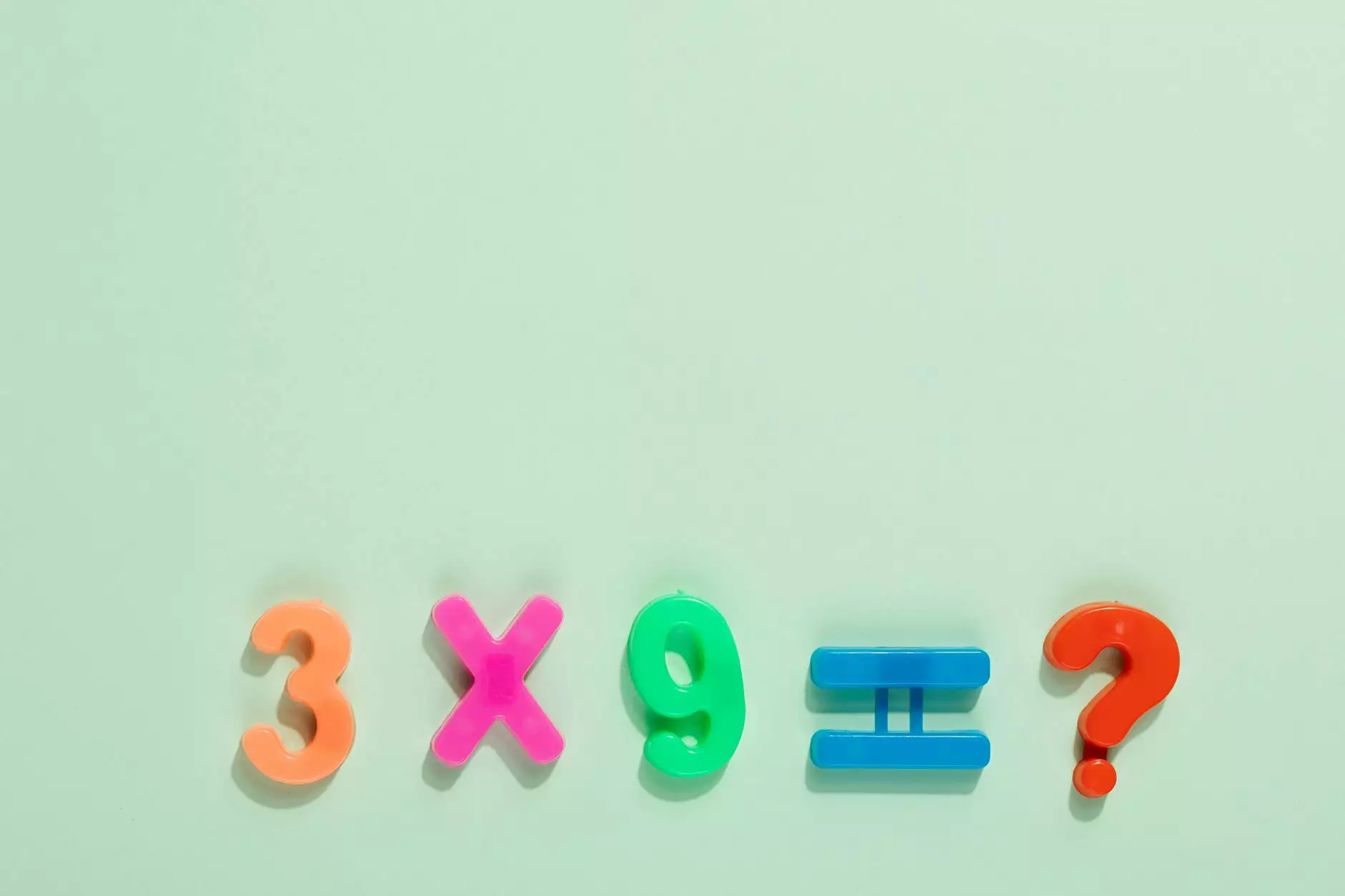
In the ever-evolving landscape of manufacturing, accurate molded plastics have carved out a vital niche, fundamentally transforming industries such as automotive, consumer goods, and electronics. As businesses strive for efficiency and sustainability, the demand for innovative materials and methods becomes paramount. This article delves into the multifaceted benefits of accurate molded plastics, highlighting their role in driving profitability and productivity within the metal fabrication sector.
Understanding Accurate Molded Plastics
Accurate molded plastics refer to polymer materials that are shaped and formed through precise molding processes. These processes utilize advanced technology to ensure dimensional accuracy and consistency, essential for high-quality outputs. Companies like DeepMould.net specialize in the development and production of these materials, catering to diverse manufacturing needs.
The Key Benefits of Using Accurate Molded Plastics
1. Enhanced Precision and Quality
One of the most compelling advantages of accurate molded plastics is their ability to achieve exceptional precision. Advanced molding techniques such as injection molding and blow molding allow manufacturers to produce components with tight tolerances. This precision translates to:
- Improved functionality of products.
- Increased customer satisfaction due to high-quality standards.
- Reduced need for additional machining or finishing processes.
2. Cost Efficiency in Production
The integration of accurate molded plastics into production processes can significantly reduce costs. Here’s how:
- Reduced Material Waste: The precision of molded plastics means there is less material wasted during production.
- Lower Labor Costs: Efficient molding processes reduce the labor required for assembly and finishing.
- Energy Efficiency: Modern molding machinery is designed to be energy-efficient, further cutting down operational costs.
3. Versatility of Applications
Accurate molded plastics are incredibly versatile, making them suitable for a wide range of applications across various industries. Some notable examples include:
- Automotive Parts: Lightweight, durable, and customizable for various vehicle models.
- Consumer Electronics: Sleek and durable casings for smartphones, tablets, and other devices.
- Medical Equipment: Biocompatible plastics that meet stringent health standards.
4. Innovation and Design Freedom
The ability to mold plastics accurately allows designers considerable creative freedom. They can create intricate shapes and forms that would be challenging or impossible with traditional materials, such as metals. This capability leads to innovative product designs that can:
- Enhance usability and functionality.
- Attract consumers with unique aesthetics.
- Facilitate advanced engineering solutions.
Environmental Considerations
As sustainability becomes increasingly crucial in manufacturing, accurate molded plastics offer a more eco-friendly alternative to traditional materials. Here’s how:
- Recyclability: Many thermoplastics can be recycled, reducing landfill waste.
- Lower Carbon Footprint: Efficient production processes translate to lower energy consumption and emissions.
- Lightweight Properties: Using lighter materials can enhance fuel efficiency in vehicles.
How Metal Fabricators Can Benefit from Accurate Molded Plastics
Metal fabricators can significantly enhance their production capabilities by integrating accurate molded plastics into their offerings. Here are several ways these materials can benefit metal fabrication businesses:
1. Complementing Metal Components
Molded plastics can be used in conjunction with metal parts to create hybrid products that take advantage of the best properties of both materials. This synergy can lead to:
- Enhanced durability and performance.
- Reduction in overall product weight.
- Cost-effective solutions that maintain high quality.
2. Faster Prototyping
The rapid nature of injection molding technologies allows for quicker prototyping of new designs. Metal fabricators can utilize accurate molded plastics for:
- Testing concepts before committing to metal fabrication.
- Speeding up the development cycle.
- Achieving market readiness faster than competitors.
3. Expanding Product Lines
By incorporating accurate molded plastics, metal fabricators can expand their product offerings without significant capital investment. This can include products like:
- Plastic housings for electronic components.
- Customized packaging solutions.
- Replacement parts that are faster and cheaper to produce.
Future Trends in Accurate Molded Plastics
The future of accurate molded plastics is promising, with several trends likely to shape the industry:
1. Advancements in Technology
Continued innovation in molding technology will increase the efficiency and quality of plastic molding. Key developments include:
- Automation and robotics in molding processes.
- Smart materials that respond to environmental changes.
- 3D printing technologies that incorporate molded plastics.
2. Sustainable Practices
As environmental concerns grow, the industry is shifting towards more sustainable practices, such as:
- Utilizing biodegradable plastics.
- Improving recycling technologies for molded products.
- Reducing the carbon footprint through improved manufacturing practices.
Conclusion
In conclusion, accurate molded plastics offer an array of benefits that can significantly enhance the manufacturing process across various industries, particularly in metal fabrication. As companies continue to seek efficiencies and innovations, these materials will play an increasingly critical role in driving productivity, quality, and sustainability. By partnering with experienced providers like DeepMould.net, businesses can leverage the advantages of molded plastics to stay competitive in a rapidly changing market.
Call to Action
For businesses looking to explore the potential of accurate molded plastics, it's essential to engage with experts who can provide tailored solutions. Visit DeepMould.net to learn more about how precision molding can transform your manufacturing capabilities today!